Cycloidal Gearbox
Samsung Botchef
During the development of the BotChef robotic arms, we needed a compact, inline, zero backlash actuator to achieve our design intent. The design and manufacture of this system became one of my major contributions to the BotChef project. After researching appropriate mechanisms and available off-the-shelf options I determined a custom cycloidal gearbox design could best fulfill our needs. Over the course of the project I designed, prototyped, and implemented multiple iterations into the v.2 and v.3 BotChef arms.

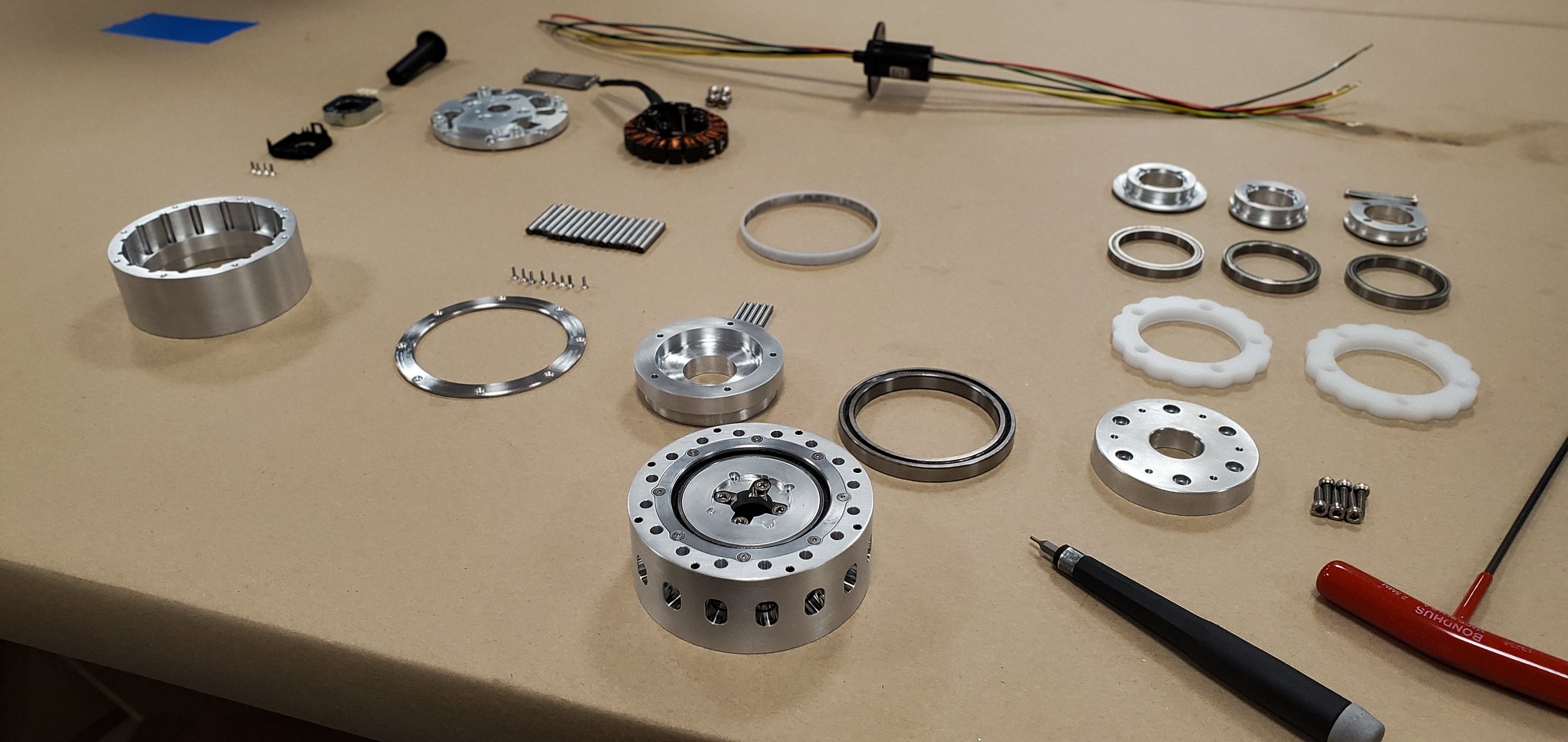
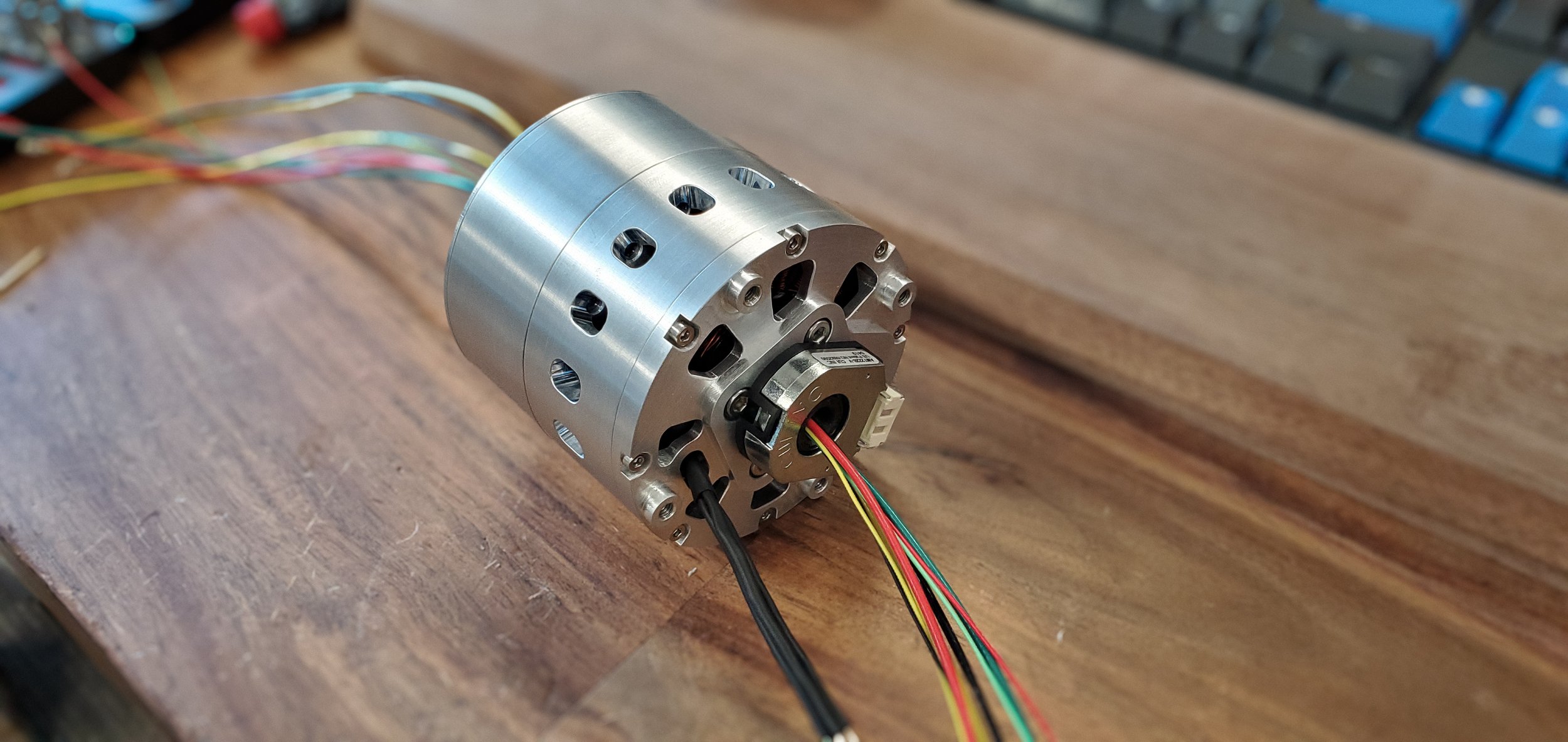
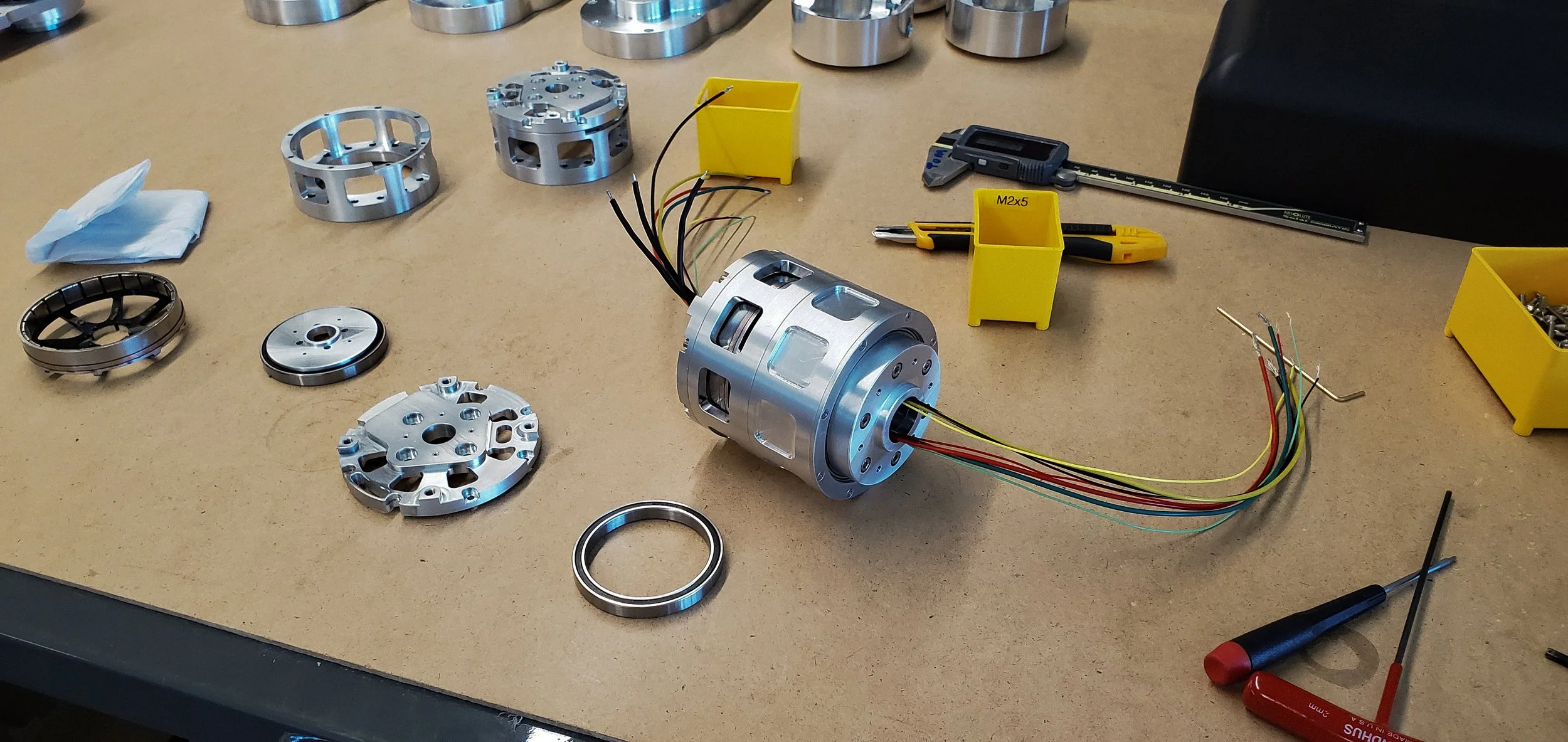
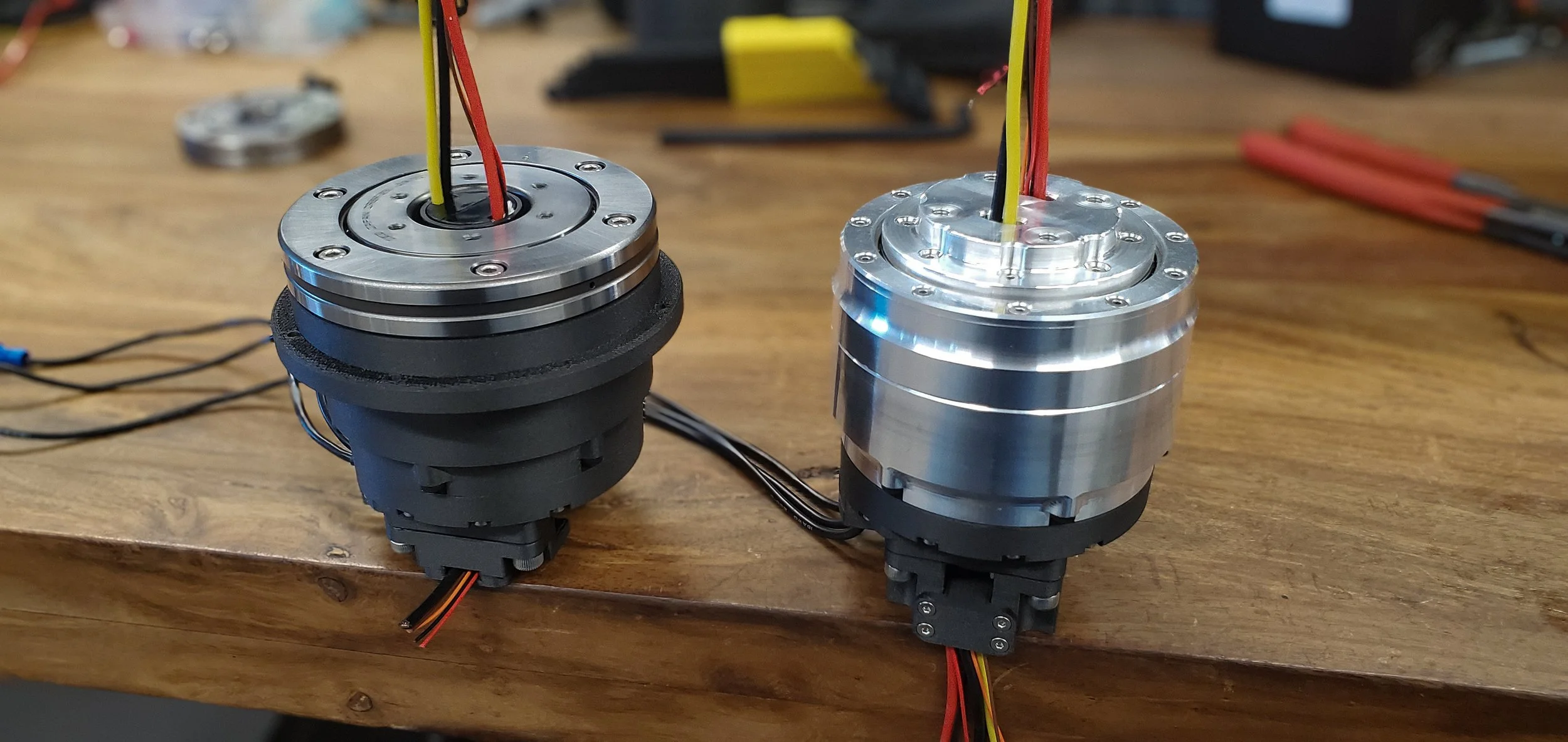

Iteration
Beginning with 3D printed explorations to validate the design I developed multiple iterations of the cycloidal gearbox design. The intent was to achieve as small a form factor as possible while meeting our requirements for wire passthrough, power, and accuracy. In addition to the cycloidal reduction, the final design integrated a slipring for power and data passthrough, a brushless motor, a custom hall effect sensor PDB for motor commutation, and a Renishaw encoder for position control. Over its iterations, I was also able to shrink the size of the actuator by approximately 10%, enough that this component was no longer the constraining factor in the arm diameter.


CAD
Pictured here are CAD images of the final cycloidal gearbox design, of which there were two slight variations for use in two of Botchef’s rotary joints. Note: Fasteners not shown.
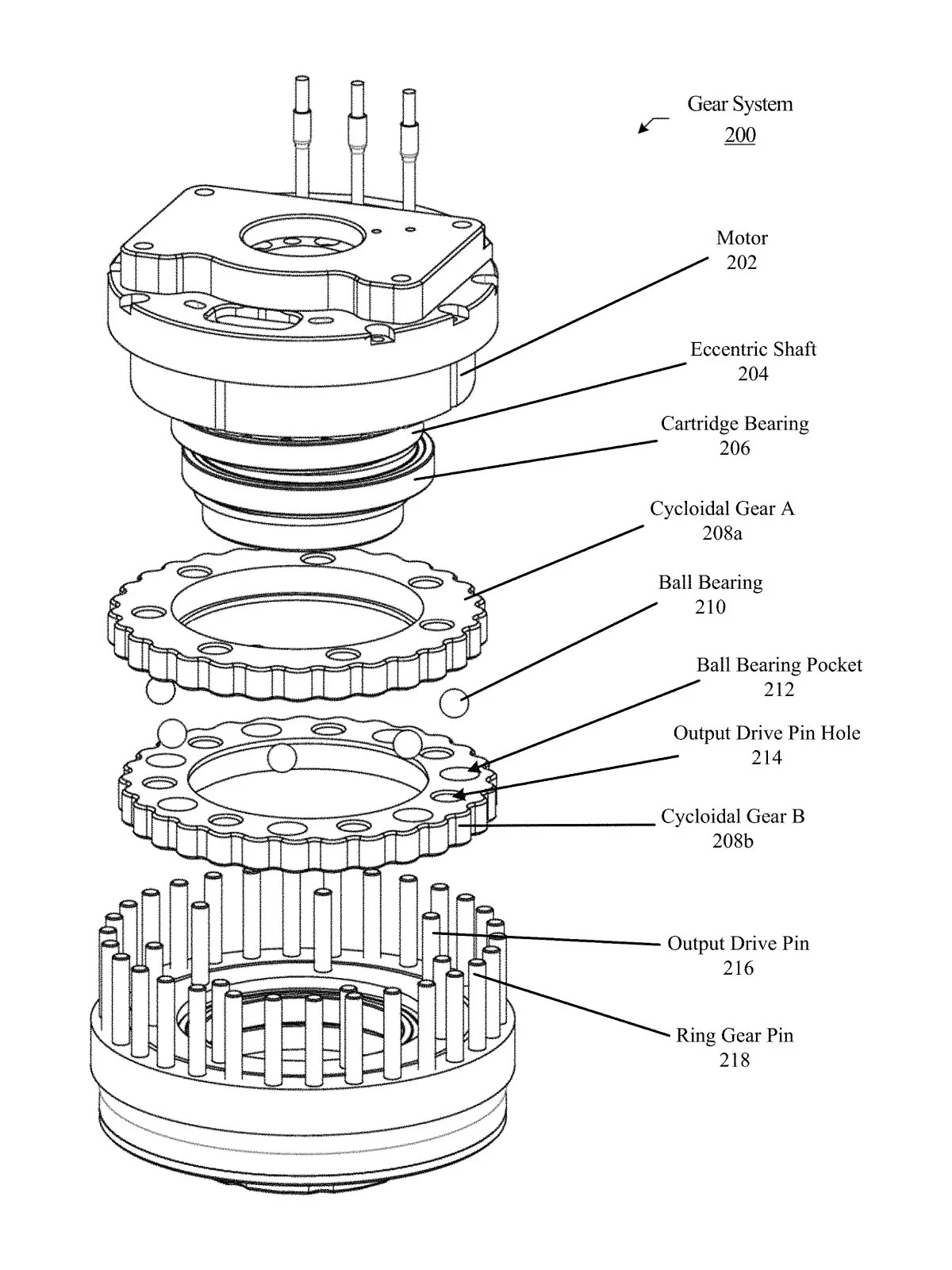


Patent
During the development of the cycloidal gearboxes, I invented a way to help constrain the cycloidal disks within a limited space. As well as a concept for using multi-material 3D printing to improve the characteristics of the cycloidal disks. Samsung applied for a patent on 4/6/2021 to cover these inventions, they were granted a US patent on 1/17/2023 under: US11554480B2